Dirty Hands, Open Mind
ASG Process Engineer Dale Hrachovec designs systems and follows them into the field to make sure they work. Here’s how he does the hot and difficult work that keeps ASG clients’ projects moving.
Dale Hrachovec is a builder and problem-solver. He puts his background in electrical engineering and experience in industrial automation to work to help ASG clients accelerate their project cycles and cut down on cost and time.
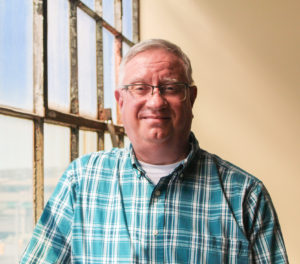
From power generation to industrial control systems and embedded software, Dale knows how to engineer and program systems that may be invisible to most people. In this Q&A, he shares insights on his experiences helping clients solve problems and how Industry 4.0 and smart, connected devices are improving the medical device industry.
Tell us what you do as a process engineer.
I engineer and design systems and then I follow them into the field to make sure they work. This is what I’ve spent most of my life doing, and this is what I do for ASG. Doing it this way doesn’t allow me to pass the responsibility to others. I fix the issues with my system and, in the process, learn how to create better solutions.
At some point all designs have to be built. Everything has to be built. Once it’s built, it has to be verified that it was built correctly. There’s been a traditional underappreciation of the skills it takes to advance a design to where it actually works. It requires a different focus and skill set.
I don’t sit behind a desk. I work to advance things from their theoretical design to an actual operating system, and I get my hands dirty during the process.
I sometimes refer to what I do as the “blue-collar side of engineering” because it’s not glamorous — it can be hot and difficult work. I don’t sit behind a desk. I work to advance things from their theoretical design to an actual operating system, and I get my hands dirty during the process.
How does your background in innovation help clients?
If a client is stuck in a development rut, it’s often because they’re working within their level of comfort and within a context someone gave them. Innovation allows me to challenge those rules and move walls that many think can’t be moved in order to create better solutions. For example, I have techniques that will cut down on the time of testing and execution. If a client needs to achieve a higher velocity through their cycles, I can help with that. There are things you can do in the design phase to accelerate your testing. Sometimes these things can be hard or cost more money. That’s why I like to get involved on projects at the front end to make sure that each step works to gain more and more velocity, which can shave weeks and months off client project cycles.
My background in innovation and designing new custom solutions really helps with that. I have a handful of methods and techniques that can systemically accelerate the development of industrial systems and embedded software in smart, connected products.
Many systems we use in daily life are invisible, and we take them for granted. Like the electricity in your house—most people don’t even think about where the power comes from. We just flip on a switch and the lights come on. They likely pay no attention to it unless it doesn’t work. I’m familiar with these concepts of invisibility, and I’m comfortable working with systems that you can’t really see. It colors how I see the world, and it shapes what I do at ASG.
Tell us more about how your skills in electrical engineering come into play?
Electrical engineering was a key to a door, but I didn’t know which door it would open. Turns out it was a key to many doors. It opened the door to things like embedded software in smart, connected products and industrial automation. It gave me opportunities to expand off the basic electrical engineering curriculum and into all those other fields. It gave me the prerequisites and allowed me to advance my career over time.
When I graduated college, I also had some programming experience. That’s how I paid for my college: I worked on programming when personal computers were invented. With the degree and the programming experience, I was a natural fit for industrial facilities. They had all this software they were in the process of creating for automated manufacturing. They needed someone to work on the software, someone who could design the wiring for the machines, and someone who could program it when they were done. I had experience doing all those things, and this is where Industry 3.0 happened (often called the computerization/automation of manufacturing).
What is industrial networking and why is it important?
Networking is the new infrastructure. Traditional infrastructure includes sewage, water and electricity. We tend to take those for granted. We turn on the switch, we get light. We turn on the faucet, we get water. Networking has become another infrastructure for systems to enable data and information for faster, better decisions. It’s invisible and no one pays attention to it. It appears to be simple on the surface; plug it in and it works. The reality is that it’s a highly critical infrastructure that people tend to overlook. We care about security, reliability and sufficient capacity in the infrastructure so clients can focus on what’s important.
For example, when you’re working on a laptop, and you see the spinning circle telling you to wait because the computer is doing something. The program might take a few seconds longer than normal, but it goes away and you keep working. This two-second delay made little to no difference to the outcome or your work product. A two-second delay on a piece of industrial machinery, however, could be detrimental and have significant impacts on performance.
Tell us more about your work in automation and software.
A huge part of our mission at ASG is client success, and there are multiple steps along the way to achieving that success. Helping clients with their automation and software development is one of those steps.
We help clients decide what to build and advance it through the manufacturing ring. Along the way, we also help improve their overall system processes as well as their manufacturing automation processes.
When a client reaches a point of asking, “Is our automation adequate for our manufacturing process?” that’s where I get involved. My goal is to mentor people on our team to understand these processes and how to improve them so that we have more capacity to help across all projects.
I hear a lot about Industry 4.0. What are your thoughts on this fourth industrial revolution?
The concept behind Industry 4.0 is getting the decision-making down to the lowest common denominator. What we’re used to is the standard command of control hierarchy where a CPU (central processing unit) makes all the decisions, and it tells other devices what to do.
Industry 4.0 has introduced a new concept when it comes to connected devices. Instead of the CPU telling each unit what to do, each unit makes its own decisions, and the CPU monitors them. The sensor makes the decision, broadcasts a signal and the actuator acts on that decision.
Before Industry 4.0, this process was wired. Now we have networking to make these processes run. This is the area I work in.
What are connected devices and how will they affect patients and medical device manufacturing in the future?
A connected device starts first with the medical device, like a glucose monitor, for example. Its purpose is to monitor glucose levels. But that’s not a connected device in itself. It becomes connected when it sends data to another device, like a smartphone or any other external device.
This raises the concern of cybersecurity. The data from the glucose monitor goes to their smartphone, but then what? Where does it go? Who receives the data? The insurance company that likely paid for the device? The device manufacturer? The patient’s doctor? Now we have questions of security and ethics. These are some of the issues that connected devices raise.
I believe the future state is smart, interconnected medical devices (i.e. glucose monitor, BP monitor, insulin pump) that all talk to one another and work together to provide the best care for the patient.
What do you like most about working at ASG?
It starts with Doug Koeneman. I’ve known him for 22 years. We worked together at another automation company at first, then went on our own paths for a while. Then I had the opportunity to come back and work with him again, and, of course, I took it. He’s a fantastic visionary and manager. If I’m working on a project, Doug is always interested and wants to know how everything is going. He’s not afraid to get in the trenches with us.
Second, I want my solutions to make a difference. ASG gives me the platform to do that. I want my work to impact people’s lives in a positive way. I’m most interested in figuring out what I can do to advance the industries we serve at ASG and to leave something positive behind. I want my work to mean something.
Currently, I’m working on establishing a new way to write software that enables faster, more automated testing and verification. This is exciting because when I get done, we can use it on connected devices and see if it works.
What do you do when you’re not at work?
Pretty much the same thing I do at work. Right now, I’m developing a new type of water sensor that detects moisture in the ground and tells us how much is there. Current irrigation systems run on timers but think about how much water could be saved over time if we only watered when it was necessary. I’m working on the algorithm to determine how wet is wet and how dry is dry. At what point is the irrigation system triggered to water the soil? This could be used for commercial and residential lawns, golf courses, businesses, etc.
I like to invent other fun devices in my spare time. Last year, I built a pair of audio-tracking cat ears for my fiancée’s Halloween costume. Tinkering and inventing are my passions.